Four ways manufacturing businesses can improve operational efficiency
8/12/2020 - CMTC
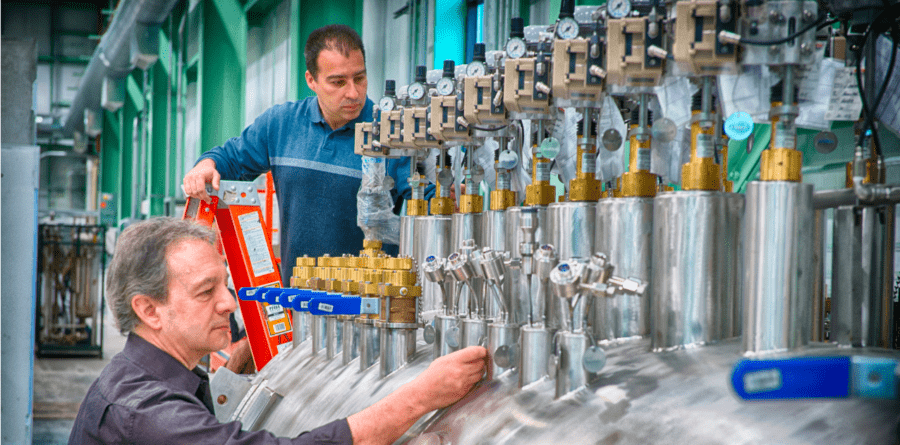
Every business wants to operate as efficiently as possible. Unfortunately, this is often easier said than done. In a manufacturing business, you can’t afford to rush into decisions that might undermine the safety of your workplace.
Below are four tips that can help any manufacturing business to improve its efficiency without compromising the quality or integrity of its operations.
Embrace Lean Manufacturing
Lean manufacturing is all about finding ways of doing more with less. Every business needs to consider the allocation and use of resources. Whether those resources are raw manufacturing materials or stationery, anything that a business buys through in the normal course of their operations should be conserved as much as practically possible.
Within a manufacturing business, the lean approach maximises value for customers while also reducing overhead costs for businesses. For customers, the value you provide is tied to the benefits of the products you produce. If you want to foster a loyal customer base, you should be looking to maximise the value you provide.
However, providing more value will usually require a business to invest more money and resources into improving their products. Under a lean approach, businesses look to add value in other ways. For example, improving your customer service and support protocols so that you are providing customers with a higher level of service along with the products you sell will add value without requiring a significant investment.
Plan Your Layout Carefully
The physical layout of any industrial operation is an important factor in determining operational efficiency. A poor layout will make your warehouse difficult to navigate and slow down your workers. Once products roll off your manufacturing line, they need to be stored appropriately. They must be easily accessible to any of your workers who need them.
An efficient layout won’t just enhance the efficiency of your manufacturing line; it will also improve the safety of your workplace. Many businesses have been embracing open-plan layouts in their workplaces; it’s all the rage right now. But there are drawbacks to an open-plan approach, especially in a manufacturing business. It makes much more sense to divide your premises into sections. For example, it is a good idea to create a dedicated reception area for visitors and deliveries. This reception area should be kept relatively isolated from the more disruptive parts of your business.
PVC strip curtains make for effective and versatile barriers within your manufacturing business. Using PVC door curtains in place of interior doors enables you to section off different areas of your business without impeding the movement of staff and goods through it. Discount PVC Curtains can provide you with an instant online quote for industrial plastic curtains. Simply enter the appropriate dimensions and select the other options you need for your PVC strip curtains and Discount PVC Curtains will generate a quote for you instantly.
Prioritise Return On Investment
The expected return on any investment should be a key consideration when you are assessing whether a particular course of action is worth it or not. It is difficult or even impossible to assess the value of an investment if you don’t know what the predicted return is.
Every business goes through some form of wear and tear over time. Even a paper supply company operating out of the same building for decades will have to periodically change their approach, invest in new equipment, and hire new personnel.
Manufacturing businesses tend to ‘age’ faster in this respect. If you have heavy machinery running for most or all of each day, it will eventually need to be replaced. Whether it’s individual components or entire machines, maintaining industrial equipment is an inevitable part of any manufacturing business.
But just because a purchase is essential or unavoidable, that doesn’t mean you should forget to maximise its value. An accurate assessment of the expected ROI will make it easy to decide whether a purchase is in your business’s best interests.
Assess Your Sourcing Protocols
It pays to have a set process in place for sourcing new equipment and resources. Many manufacturing businesses are wary of buying second-hand equipment. However, this is an effective way of keeping costs down.
If you have a clear set of policies in place, anyone who might need to place orders for your business will have the confidence to do so without running it by senior management beforehand. As a result, you can get any new equipment you need to be delivered and installed as quickly as possible.
Efficiency is a prominent concern for any business. Manufacturing businesses are far from unique in this regard. However, the challenges that manufacturing businesses face in improving operational efficiency are unique. Poor decision-making can undermine the safety and efficiency of your business. The tips above will help you to make smarter and more reliable operational decisions.
For more information please visit the CMTC website
All articles on this news site are submitted by registered contributors of SuffolkWire. Find out how to subscribe and submit your stories here »